
«Designed for manufacturability»
~ CoroDrill® 860 solid hardmetallbor støtter innovativ produksjon ~
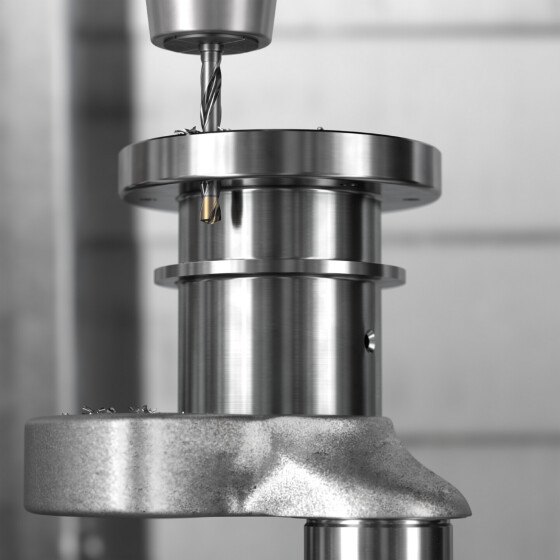
«Det er ingenting som er effektivt med innovasjon» sa den britisk-amerikanske forfatteren og foredragsholderen Simon Sinek. Men har han rett? Det er opp til produsentene å innovere og holde tritt med endringene, særlig de som drives frem av e-mobilitet. Her forklarer Robert Smith, «Offer Manager» for «Hole Making & Composites» i forretningsenheten «Solid Round Tools» (SRT) hos spesialisten på skjæreverktøy, Sandvik Coromant, hvordan produsenter kan - og må - ha en effektiv innovasjon med avanserte hardmetallbor.
«Design for manufacturability» (DFM) har blitt stadig viktigere for produsenter i en rekke bransjer, blant annet bilindustrien, flyindustrien og innen generell ingeniørvirksomhet. DFM betyr å designe og utvikle produkter som kan produseres enklere, mer effektivt og billigere. For kundene til Sandvik Coromant tilsvarer dette som regel at de oppnår en gunstig kostnad per del når de skal «matche» komponenter, eller redusert kostnad per hull ved boring eller gjenging. Hvert av disse målene krever skjæreverktøy som er svært pålitelige og gir høy produktivitet.
DFM-konseptet er dessuten i stadig utvikling på grunn av en stadig mer globalisert forsyningskjede og økende etterspørsel etter kundetilpassede produkter. E-mobility vil også påvirke DFM. Deler til el- og hybridbiler varierer mer fra produsent til produsent enn tilsvarende deler til forbrenningsmotorer, og de lages i økende grad av slitesterke materialer som lavlegert stål, Inconel og aluminium. Mens den ventede trenden innen e-mobilitet i flyindustrien fortsatt ligger mange år frem i tid, er trenden over oss nå i bilindustrien - produsentene må holde tritt med endringene, ellers risikerer de å bli akterutseilt.
Men hvordan kan avanserte bearbeidingsløsninger gjør en forskjell DFM? Svarene finner du i fasene fra CAD-til-komponent (Computer Aided Design - dataassistert konstruksjon) i produksjonen. CAD-til-komponent kan vise til tre trinn i produksjonen. Den første fasen er en CAD-til-spindel-fase, der CAD og CAM-modeller (computer aided manufacturing - dataassistert produksjon), inkludert digitale tvillinglignende simuleringer benyttes til å gjøre alt klart til produksjon, og til å sikre at verktøyet, arbeidsstykket og maskinens parametere alle er optimale.
Den andre fasen, spindelfasen, eller selve produksjonen. Her kan vi vurdere verktøyets bearbeidingsytelse i forhold til arbeidsstykket og effekten på kostnad per del, kostnad per hull og - til syvende og sist - kundenes bunnlinje. Den tredje fasen er enkel-til-komponent-fasen, der kvaliteten og finishen på den endelige komponenten vurderes. Enten det gjelder bilindustrien, flyindustrien eller generell ingeniørvirksomhet, er finish og egenskaper som hullets overflateintegritet av avgjørende betydning. Bedre hullkvalitet forebygger komponentfeil – og avhenger i stor grad av produksjonsprosessene som brukes til maskinering eller etterbehandling av hullene.
Spesielt er borets design avgjørende for å produsere hull av bedre kvalitet. Dette er grunnen til at geometrien til skjærekanten i bor er i kontinuerlig utvikling, da det er viktig å oppfylle de høyeste standarder for produksjon og delekvalitet. Bruk av kjølevæske er også viktig for å redusere varmeutviklingen i verktøyet. Det er her spesialistene fra Sandvik Coromant kan spille en avgjørende rolle i å hjelpe kundene.
Lett å produsere
Sandvik Coromant arbeider side om side med kunden for å samle inn all relevant informasjon om prosjektene, og ser da hva som er nødvendig. La oss si at kunden har behov for å utføre en kontinuerlig boreoperasjon i et arbeidsstykke av rustfritt stål 316L — et materiale som, som vist i en undersøkelse utgitt av ARPN (Asian Research Publishing Network) i deres «Journal of Engineering and Applied Sciences», har vist seg å forårsake en «rask og dødelig slitasje» som har alvorlig innvirkning på skjæreverktøyets levetid.
På dette stadiet av kundens maskinprosess, det tidligere nevnte CAD-til-spindel-stadiet, kan våre spesialister undersøke og rekonstruere kundens prosesser ved hjelp av CAD- og CAM-modeller. For å gjøre dette kan Sandvik Coromant utvikle en prototype om morgenen, og ha denne klar til testing av FoU på ettermiddagen. I tiden før digitaliseringen måtte tegningene sendes frem og tilbake, noe som kunne ta opptil seks uker. I dag kan Sandvik Coromant levere prototyper på verktøyet samme dag, noe som har vært avgjørende for selskapet.
Økt holdbarhet på verktøy
Sandvik Coromant tilbyr en rekke produkter som hjelper kundene med å produsere komponenter, blant annet for e-mobilitet. De inkluderer CoroDrill® 860, massive hardmetallbor for rask og problemfri boring, som maksimerer produktivitet med høy metallskjæringseffektivitet. Verktøyet er tilgjengelig i en rekke geometrier, inkludert 860-MM for materialer i rustfritt stål med lang sponingstid, som austenittisk, superaustenittisk, ferritisk og dupleks rustfritt stål.
Du har i tillegg CoroDrill® 860-GM som har vist seg nyttig for bilprodusentene til boring av motorblokker, foringsrør, flenser og manifolder. Boret egner seg også til alle andre bruksområder enn bilindustrien og generell ingeniørvirksomhet, der hullkvaliteten er avgjørende - for eksempel innen romfart, olje og gass, kjernekraft og fornybar energi.
860-GM har gitt imponerende resultater, blant annet for en bilprodusent i Korea. Kunden til Sandvik Coromant skulle bore gjennomgående hull i et produksjonsparti med kontakter til biltransmisjon. Målet var å bore åtte gjennomgående hull med en diameter på 8,2 mm (0,32") i hver komponent, med en dybde på 10 mm (0,39"). Den eksisterende løsningen produserte 200 komponenter, totalt 1600 hull, med en skjærehastighet (Vc) på 80 m/min (3102 o/min) og en skjæremating (Vf) på 381 mm/min. Til sammenligning produserte CoroDrill® 860-GM 2300 komponenter (18400 hull) med en Vc på 100 m/min (3878 o/min) og Vf på 814 mm/min.
Totalt sett leverte CoroDrill® 860-GM en betydelig forbedret levetid på verktøyet, med 1150 %. Dette førte til en produktivitetsøkning som bidro til betydelig lavere kostnad per del for kunden. Tilsvarende imponerende resultater er rapportert av andre kunder hos Sandvik Coromant i bilindustrien over hele verden.
Like viktig som å bore jevne hull er gjenging, som skaper gjenger inne i hullet. Derfor tilbyr Sandvik Coromant CoroTap® 100, 200, 300 og 400, som alle er optimalisert for ulike bruksområder. For å ta et par eksempler: CoroTap® 100 er en serie rettskårne gjengetapper som er optimalisert for kortflisede ISO K-, ISO N- og ISO H materialer. CoroTap® 400 er et høy, sponfri formende gjengebor egnet for både gjennomgående hull og blindhull i stål, rustfritt stål, aluminium. Kundens valget avhenger av hvilket produkt som er det beste for deres bruksområder.
I framtiden vil Sandvik Coromant tilby CoroTap® 100-N og CoroTap® 400-N. Begge er utviklet for å hjelpe kunder med gjengeapplikasjoner i aluminium, noe som blir stadig mer vanlig i produksjonsprosesser.
Foreløpig viser ytelsen til Sandvik Coromants skjæreverktøy at verktøy som er utviklet for boring og gjenging i flere materialer, vil være avgjørende for å hjelpe produsenter med å produsere lettere, mindre og mer varierte komponenter. Ikke bare kan maskinverkstedene designe og utvikle disse delene på en enklere og mer kostnadseffektiv måte, de kan også sørge for at DFM forblir en prioritet gjennom hele produksjonen – og skape innovasjon med effektivitet.